Custom Containers | Arnold Packaging
Custom Wood Shipping Crates Built Right
Throughout our 90+ year history, Maryland-based Arnold Packaging has striven for excellence – no more so than with the custom wood shipping crates we design and manufacture for our customers in the Mid-Atlantic region.
That’s because we know how important it is that their product arrives at its destination in perfect condition and with the lowest possible shipping costs. We’d be honored to do the same for your business. Here’s how it would work…
Our Process for Designing and Manufacturing Custom Wood Crates

It all begins with a free consultation with our package engineers. They’ll meet with your team to dig deep and uncover the design for the container that best fits your needs. The tougher the challenge, the more out engineers enjoy it…
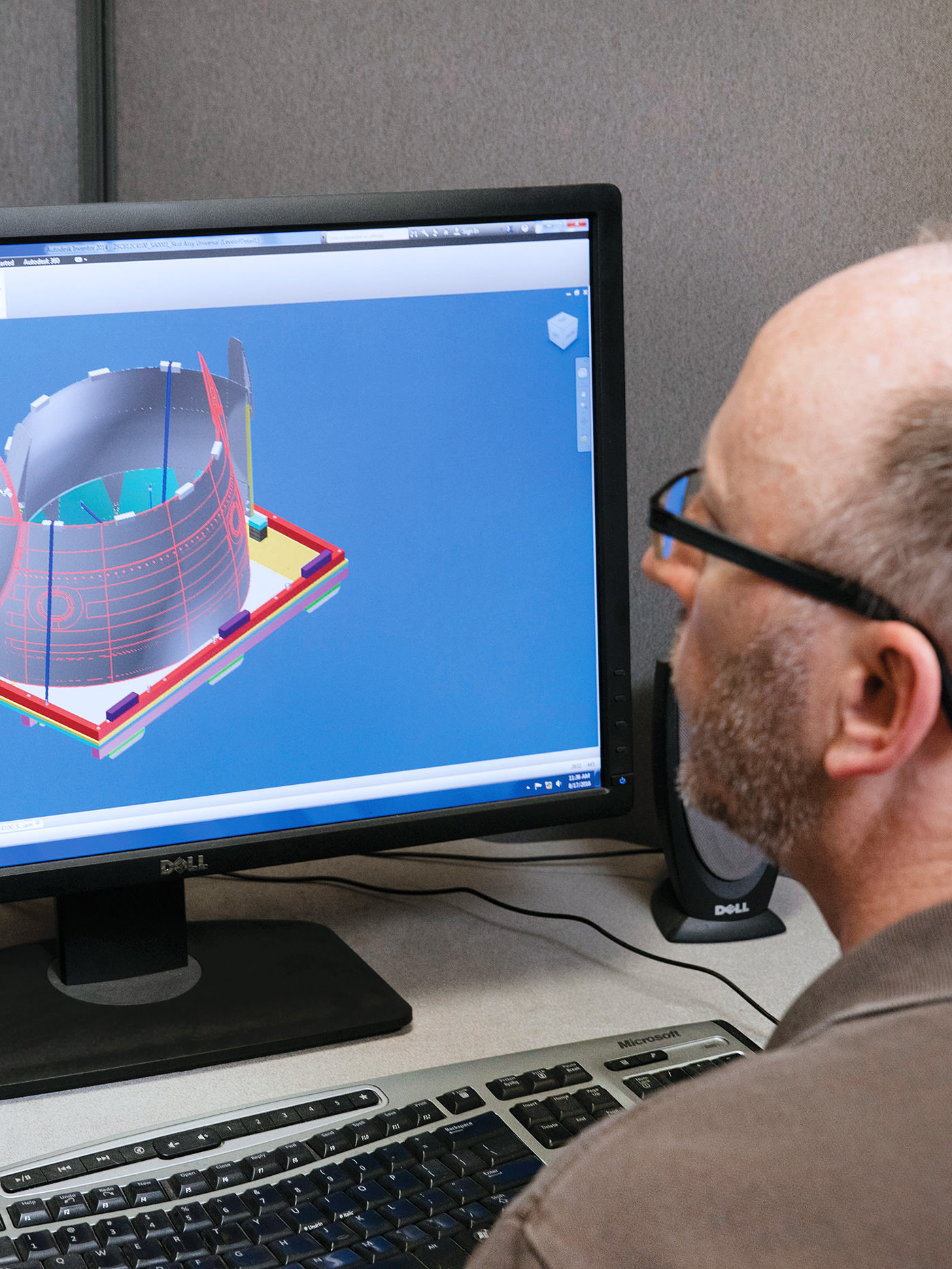
We’ll also look for ways to boost your bottom line by proposing new materials in the design that can reduce shipping weight or allow you to pack more product per shipment. (You can read a case study where we did just that right here.)
Taking a look inside the container, we’ll assess the optimal materials or method for cushioning your precious cargo. This may include features such as foam padding, shock absorption, or custom interior fittings to protect delicate or high-value items during transit.
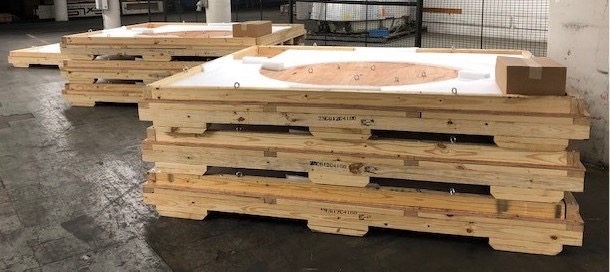
Once we’ve got the design down, we’ll manufacture the custom container using high-quality heat-treated lumber and thoroughly test it in our Sparrows Point, Maryland warehouse.
We’ll even review your equipment, workflow and logistics to offer you a total solution for optimizing the packaging and shipping component of your supply chain.
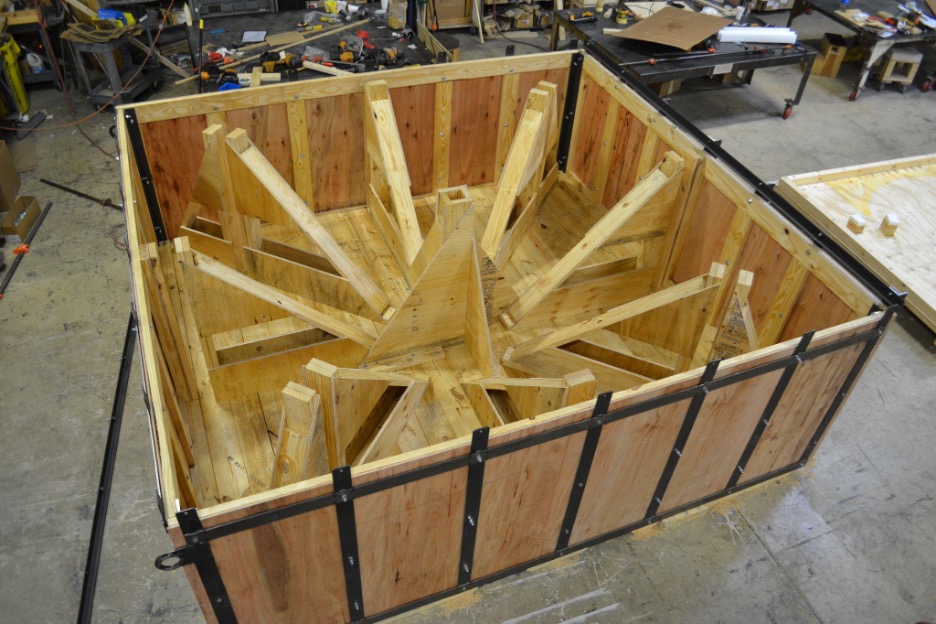
Plus, we can save you space and free up cash by not only building your container/s ourselves, but also by managing your current stock levels with our technology-driven inventory tracking and just-in-time replenishment programs.
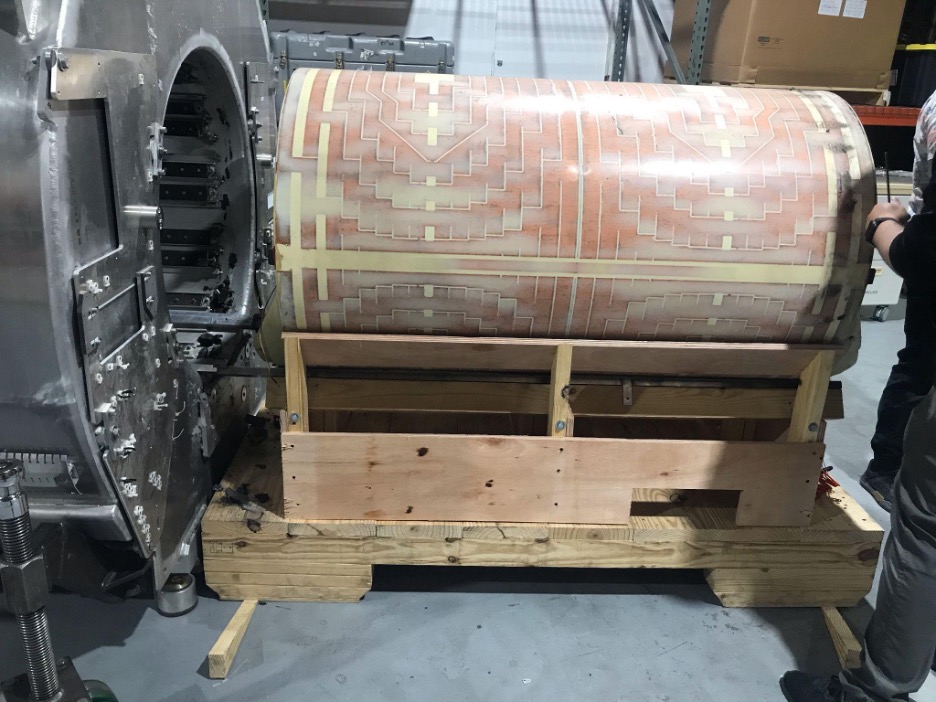
Arnold Packaging is your one-stop resource for custom wood shipping and storage crates of all kinds.
“Imagination is the beginning of creation.”
– George Bernard Shaw
How important is it to have the right shipping crate?
For a lesson in the importance of the right shipping crate, history buffs will enjoy reading about the below container in “The Wardian Case: How a Simple Box Moved the Plant Kingdom.”
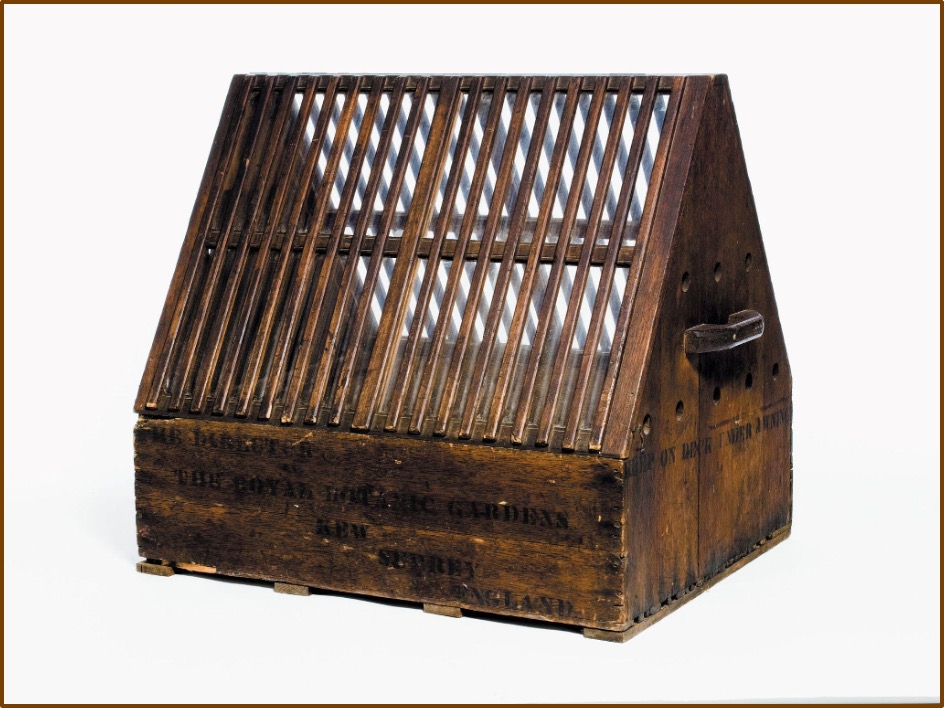
Common Types of Custom Wood Shipping Crates
Not every business requires a unique highly-designed container. Some styles are suited to a variety of purposes and industries. Here are a few common types:
Type I Crates
Type I crates are general-purpose wooden crates typically used for packaging, storing, and shipping a wide range of goods. They have solid walls and may or may not have a lid, depending on the specific requirements.
Type II Crates
Type II crates are designed to meet specific requirements for shipping and storing military equipment and supplies. They are built to withstand rough handling, transportation, and storage and are therefore popular with moving and storage companies, as well.
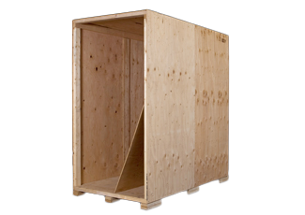
Open Crates
Open crates are wooden containers with slatted or partially open sides, providing ventilation and visibility of the contents. They are commonly used for transporting goods that do not require complete enclosure, such as fresh produce or oversized items.
Closed Crates
Closed crates have solid walls on all sides, providing complete protection and containment of the contents. They are suitable for shipping fragile or sensitive items that need to be shielded from external elements and impacts.
Collapsible Crates
Collapsible crates are wooden containers that can be folded or collapsed when empty, reducing storage space and transportation costs. They are ideal for applications where space efficiency is crucial.
Storage Vaults
Storage vaults have sturdy solid walls on all sides secured with clamps. They can be stacked and are often used by moving, storage and restoration companies for to store boxes of household goods.
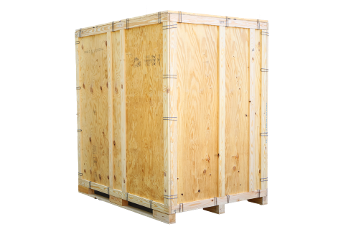
Heavy-Duty Crates
Heavy-duty crates are reinforced with additional bracing, corner posts, or metal straps to withstand heavier loads and rough handling during transportation and storage. They are used for shipping durable goods or machinery that require extra support
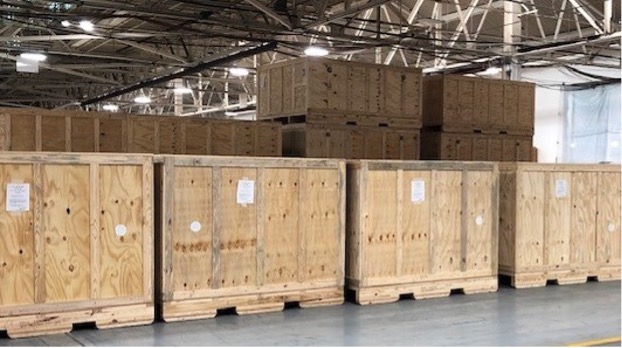
ISPM 15 Compliant Crates
Crates that comply with International Standards for Phytosanitary Measures No. 15 (ISPM 15) are heat-treated or fumigated to prevent the spread of pests and diseases in international trade. These crates are marked with the ISPM 15 stamp, indicating that they meet the required treatment standards for wooden packaging materials.
“One Size Does Not Fit All”
– Maryland-Born Frank Zappa
Ask the Experts…
What is the overall cost of shipping damage?
The costs of product damage ripple throughout an organization in both direct and indirect ways…
Storage Costs
Damaged items also require inspection and storage, consuming additional time and space. When you prorate the total costs of storing damaged goods, including property taxes, utilities, and rent or mortgage, the expenses escalate further.
Parts & Repair Costs
Some businesses choose to refurbish returned items if the damage is primarily cosmetic, which incurs labor and parts costs. Although the company may profit from selling the repaired product, the margin will be lower compared to selling a new item.
Sale Impact
Sales may also be affected. If damaged items are salvaged and sold at a discount, they compete with full-price items, potentially harming the company’s reputation. An abundance of discounted damaged goods can subtly degrade the perceived value of the brand.
Logistics Costs
Reshipping items increases logistics costs, especially if overnight shipping is necessary. This can cause delays that influence a customer’s current and future buying decisions. Depending on the severity of the damage and the customer’s overall sentiment, the company might need to go further, potentially offering a free item to compensate for the inconvenience.
“Damaged Freight Represents Lost Opportunity”
Lost Opportunities
Damaged freight also represents a lost opportunity. For example, rather than placating customers with damaged goods, sales reps could be reaching out to potential new clients. Companies could receive payments sooner, using that capital to fund additional staff, expand facilities, or launch marketing campaigns to attract new business.
Reputation Damage
Word of mouth is the most powerful form of marketing, and a disgruntled customer is especially likely to share their negative experience.
Paperwork
Filing a freight claim, for instance, typically takes about two hours, resulting in lost productivity.
By factoring in these costs, you can more accurately determine the true expenses of shipment damages for your business. While these costs will vary by product line and company, this analysis often reveals surprising insights. These outcomes can motivate decision-makers to explore further measures to minimize shipping damage.[1][2]
What types of testing are performed on customer containers?
At Arnold Packaging, we follow the industry standard: ISTA (International Safe Transit Association) testing. It involves subjecting containers, packaging, and products to various simulated transport and environmental conditions to assess their ability to withstand the rigors of distribution.
This testing helps ensure that products arrive at their destination intact and undamaged. Here’s a basic outline of the process:
Identify Test Requirements
Determine the appropriate ISTA test procedures based on the type of container, its contents, and the expected distribution environment.
Prepare Test Samples
Prepare the containers and products according to the guidelines, including packaging materials, cushioning, and any necessary instrumentation for data collection.
Perform Tests
Conduct the prescribed ISTA tests, which may include:
Random Vibration Test:
Simulates the vibrations experienced during transportation.
Shock Test:
Mimics the impacts and jolts that can occur during handling and transportation.
Compression Test:
Evaluates the ability of the container to withstand stacking and pressure.
Drop Test:
Assesses the container’s ability to withstand drops from various heights.
Environmental Conditioning:
Exposes the containers to temperature, humidity, and altitude variations to simulate real-world conditions.
Data Collection and Analysis
Record relevant data during testing, such as vibration levels, shock forces, and any visible damage to the container or product.
Evaluate Results
Analyze the test results to determine whether the container meets the required performance criteria. This may involve comparing the observed performance with established thresholds for damage or deformation.
Report Findings
Document the test procedures, results, and any recommendations or corrective actions needed to improve container performance.
Certification and Compliance
If the container passes the ISTA testing, it may receive certification indicating its suitability for transport under specified conditions. Non-compliance may require redesign or reinforcement of the container to meet the necessary standards.
_________________
[1] https://supplychainbeyond.com/true-cost-of-shipping-damage/
[2]https://www.supplychainbrain.com/ext/resources/secure_download/KellysFiles/WhitePapersAndBenchMarkReports/SpotSee/Assessing_the_Total_Cost_of_Supply_Chain_Damage.pdf
“Quality means doing it right when nobody is looking.”
How can a packaging redesign save my company money?
Here are a few examples to illustrate how a packaging redesign can protect your product – and your profits…
When a Maryland-based global provider of broadband satellite services and products faced persistent damage to their blade servers during handling, shipping, and delivery, they called Arnold Packaging. The shocks experienced during transport caused internal components to break free, rendering the servers nonfunctional.
Our packaging engineers discovered that the polyethylene foam they were using was too rigid, transmitting shocks to the unit. They redesigned the packaging using a custom Korrvu insert with a flexible, low-slip film that securely held the product in place.
The result? The redesign successfully reduced the damage rate to less than 1 percent, meeting the customer’s goal. Additionally, the cost of packaging materials per unit was lowered. Get the full story here.
“Many companies tend to overestimate the strength needed for packaging materials, leading to unnecessary expenses."
Many companies tend to overestimate the strength needed for packaging materials, leading to unnecessary expenses. Through two testing procedures, we found that reducing the weight of each box by two one-hundredths of a pound would still maintain necessary strength and durability. This change results in an annual weight reduction of nearly 20 tons.
- Static Stacking Strength Testing: We calculated the stress boxes would endure when stacked in the warehouse. For our client, who stacks 790-pound pallets four high, we needed to ensure the bottom boxes could support the weight above them. We analyzed specifications for different linerboard combinations, entered the data into a software application, and used the safety factor provided to guide our design.
- Parcel Testing: After arrival at the distributor, pallets are usually shipped via UPS or FedEx. We used the International Safe Transit Association test 1A (ISTA-1A) to simulate transit conditions (as described above).
Armed with this data, we redesigned the client’s box to be lighter without compromising performance. This minor weight reduction translated to a 4.34% reduction in materials used and a 9.8% cost reduction for the client. Get the full story here.
At Arnold Packaging, it’s our mission to protect your product and your profit. Complete this quick form to schedule a free consultation. You can also reach out to me directly at the number or email below.
Jacob Van Brunt
Packaging Engineer
C: 443-909-6386
jvanbrunt@arnoldautomation.com
Jacob has a degree in mechanical engineering and enjoys finding new and inventive ways to help customers improve packages cost, safety and packability.
Custom Containers News
No-Cost Packaging Analysis
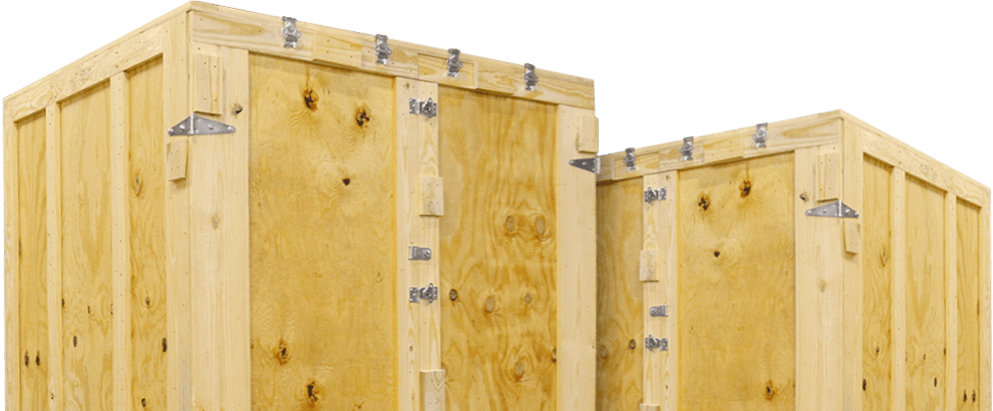